The water industry in Asia, especially Singapore, has been booming, thanks to global pharmaceutical companies moving their operations to the region to be closer to their customers. Even as electronics manufacturers moved out of Singapore, beginning in the 1980s, pharma firms have moved in to fill the demand for high quality water, which is driven by strict regulations from the likes of the European Union.
According to the US research firm IMS Consulting Group, the region’s pharma market is expected to reach US$350 billion in 2016, accounting for 30 per cent of the global pharma market and driving close to 50 percent of global growth through 2016. Asia is therefore becoming an increasingly importance manufacturing base for the pharma industry.
The fact that the city is home to more than 170 water companies – involved in everything from research, design, treatment and manufacturing – is definitely a boon for these drug-makers.
From electronics to pharma
Indeed, Veolia Water Technologies has seen the pharmaceutical and healthcare segment in Southeast Asia grow by “a few hundred percent” over the past decade or so.
Veolia Water Technologies, which has its Southeast Asian headquarters in Singapore for the Industrial activities, has witnessed first-hand the shift to pharmaceutical manufacturing from electronics production in Singapore during the three decades it has been based in the city.
Manufacturers such as Seagate, IBM and Samsung all moved their factories to cheaper locations elsewhere in Southeast Asia such as Malaysia and Thailand.
“We were among the biggest suppliers of pure water to the microelectronics industry in Singapore and Southeast Asia during the 80s and 90s, and there is similarity in the requirements for the pharmaceutical industry even though validation protocol is very different,” says Chiang Heng Kheng, business development director, solutions business line, Singapore & Indonesia for Veolia Water Technologies.
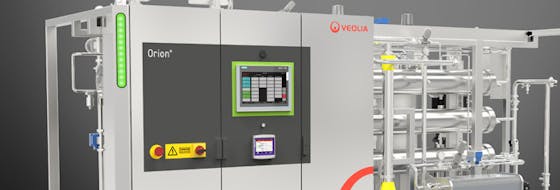
Veolia Water Technologies’s Orion System
“These similarities allowed us to adapt to become a key supplier of water to the pharmaceutical industry when the shift happened in the 2000’s,” Chiang adds.
Chiang oversees the pharmaceutical business of Veolia Water Technologies in Singapore and Indonesia – and increasingly the rest of Southeast Asia – where many customers are European and American drug makers. These multinational firms typically require all their production sites to operate in the same way and meet the same stringent standards.
Within the pharmaceutical industry, water is used not only as an ingredient in many formulations but also as a cleaning agent. Production of different grades of water such as Purified Water, highly Purified Water, Pyrogen Free Water and Water-for-injection (WFI) to international pharmaceutical standards is widely recognised as a critical process. The water is usually produced in-situ at the pharma manufacturing facility, using local potable water – which is itself obtained from natural water sources and treated by various processes.
This is where Veolia Water Technologies (Asia Industrial), which has 700 employees in Southeast Asia, has an advantage. It not only is able to tap into the research and development expertise of its global parent in Paris, it also has well-trained local engineers to implement projects throughout the region.
“We are very globalised but our teams, operations managers and engineers are local,” Chiang says. “This means that we can tap into the expertise of our colleagues overseas anytime, but we also understand very well the demands of the region.”
This is why Veolia Water Technologies’ customers tend to be repeat clients who commission the company to design multiple sites, he says.
Global standards
No matter the application - pre-treatment, purification, storage and distribution or wastewater treatment – Veolia’s solutions help improve manufacturing efficiency and reduce costs,
“
Consistency is one of the biggest requirements of the pharmaceutical industry. Also, customers want their suppliers to comply with their sustainability efforts, which usually extend to all their global sites.”
Chiang Heng Kheng, business development director, solutions business line, Singapore & Indonesia for Veolia Water Technologies.
The pharmaceutical industry, in particular, needs purified water to make eyecare products, antibiotics, veterinary products, and other uses such as tablet-coating, granulation, and diagnostics.
This is done by Veolia’s Orion system, its flagship water-treatment technology that’s tailored for the pharmaceutical industry.
One customer that has installed Orion at multiple sites is a multinational consumer goods manufacturer which was expanding in Asia and wanted its production sites around the world to operate to the same high standards.
From December 2013 to July 2014, Veolia designed and installed three water treatment plants – costing more than 3 million euros – in India and China for the customer, whose name cannot be disclosed for commercial reasons. These plants treat raw water to meet the highest specifications and wastewater before it is discharged to the waterways.
Another customer, a global leader in eye care, required water of a specific pharmaceutical quality for its new production site in Singapore. It was also looking for an environmentally friendly and efficient solution to handle its wastewater.
Veolia designed a system, also based on its Orion technology, that provided the customer with highly purified water which is fully compliant with global manufacturing and health standards. Any wastewater was also treated before being discharged and the by-product collected for proper off-site disposal.
Another key feature of Orion is that it can be linked to Vision, a web-based customer portal also offered by Veolia that allows access to all information regarding Orion, its products and services.
Vision also allows for remote monitoring and access to real-time encrypted performance data 24 hours a day, including alarms that alert users to any irregularity in the Orion system and equipment status.
This enables easy control of the system at all times - something Veolia’s customers requested.
“Consistency is one of the biggest requirements of the pharmaceutical industry,” Chiang says. “Also, customers want their suppliers to comply with their sustainability efforts, which usually extend to all their global sites.”
For example, when French cosmetics giant L’Oreal wanted to ensure that it had zero chemical waste discharging into waterways and landfills at all of its 43 factories across the world , it enlisted Veolia to design a wastewater treatment system.
Veolia worked with L’Oreal on the design and construction of the wastewater plant such that it also fulfilled the requirements of the United States Green Building Council’s LEED (Leadership in Energy & Environmental Design) ratings system (in reference to L’Oréal Plant in Indonesia who received the first Leed Silver Certification in Indonesia).
“We are completely linked to the needs of the market,” Chiang said. “We can offer flexibility in our standardised solutions for our customers and make things simple for them to meet their sustainability and operational goals.”