The Singapore-ETH Centre and United World College Southeast Asia (UWCSEA) have unveiled a ground-breaking technology that allows three floors of offices to be built within the standard space of two.
To continue reading, subscribe to Eco‑Business.
There's something for everyone. We offer a range of subscription plans.
- Access our stories and receive our Insights Weekly newsletter with the free EB Member plan.
- Unlock unlimited access to our content and archive with EB Circle.
- Publish your content with EB Premium.
The collaboration between urban research institute Singapore-ETH Centre Future Cities Laboratory (SEC FCL) and UWCSEA was announced on Wednesday at the institute’s premises on the National University of Singapore campus. When completed in mid-2015, it will be Singapore’s most energy efficient office, say its creators.
The office, located in UWCSEA’s new building in western Singapore, will feature SEC FCL’s ‘3for2’ technology, a cutting-edge concept that enables builders to save on space, building materials, energy consumption, and costs by allowing building developers to construct three floors within the height required for two stories in conventional buildings. This is achieved without any impact on perceived floor to ceiling heights. It is the first commercial application of the 3for2 concept, which had previously only been used in small-scale pilot studies.
In addition to saving space, the system also reduces energy consumption by up to 40 per cent, a feat that is achieved by separating the cooling and dehumidifying functions of conventional air conditioning (air-con) systems.
Arno Schlueter, project leader and chair for architecture and sustainable building technologies at the Swiss Federal Institute of Technology (ETH) Zurich, explained that conventional air-con systems are extremely inefficient because the air running through the systems need to be cooled down to 6°C in order ensure that its humidity levels are at a comfortable 60 per cent when it is channeled into the room. The temperature then has to be raised to about 20°C in order to cool the indoor environment.
Schlueter added that in addition to the energy wastage resulting from cooling all the air in a building’s ventilation system to such a low temperature, conventional models also require bulky ducts to circulate the air. This is not an ideal system because not only is air an inneficient carrier of heat, the ducts also occupy one-third of the volume in a building’s interior.
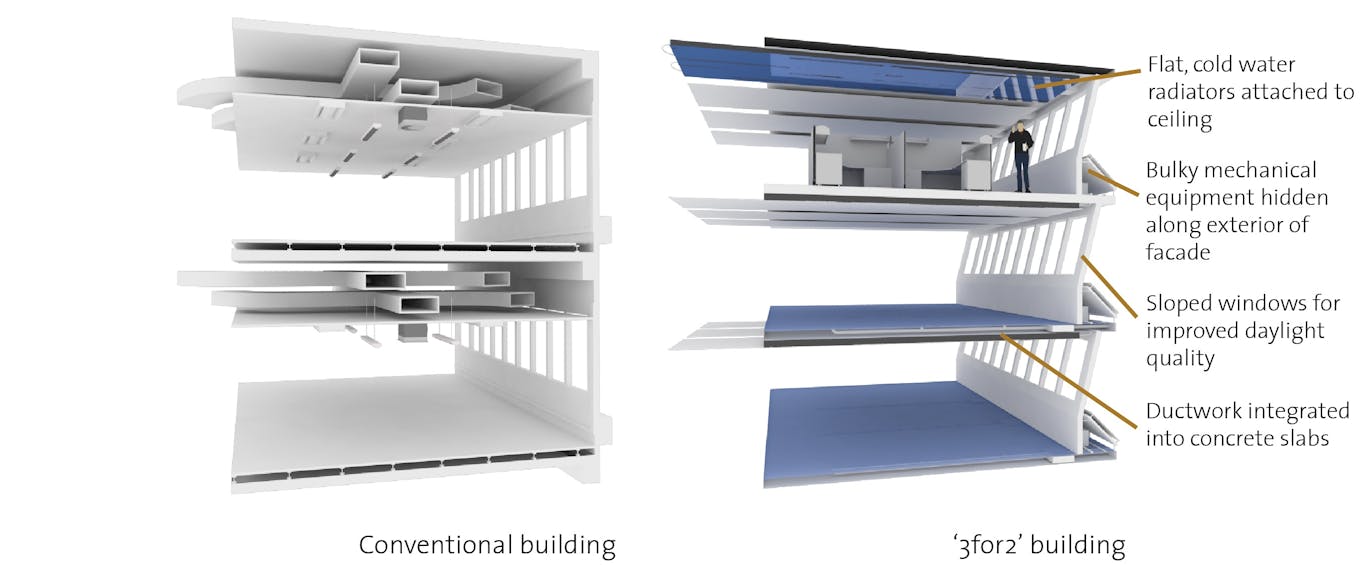
A comparison of conventional building design versus the 3for2 concept, which allows developers to construct three floors within the standard space of two floors by removing the need for bulky air conditioning ducts in ceilings. Image: SEC-ETH Centre Future Cities Laboratory
“
If a new set of solutions for air conditioning and lighting could halve both space and energy requirements, we could achieve significant savings to building material costs and energy bills. This combined cost savings potential has been largely untapped by the green buildings sector thus far.
Arno Schlueter, leader, 3for2 project
To address these inefficiencies, the 3for2 system carries out dehumidification and cooling separately. In the single-purpose dehumidification unit, the amount of air that needs to be cooled down to 6°C to is reduced by 40 per cent compared to conventional systems.
Meanwhile, the cooling function of air-conditioners is replaced by passive chilled beams (PCBs), which are flat, cold water radiators attached to the ceiling which cool the surrounding environment through heat transfer.
This is a much more efficient system, because the water in the radiators only needs to be cooled down to 18°C to bring about a comfortable temperature for occupants, said Schlueter.
Adam Rysanek, project manager of the 3for2 initiative added that since the new office facility will only occupy one floor of the UWCSEA building, the PCBs would be cooled with chilled water that has already passed through the rest of the building’s cooling system, but is still cool enough for use in the PCBs. This would enhance the office’s resource efficiency, said Rysanek.
Additional energy saving features in the office included sloped windows to improve the quality of daylight while reducing heat gain through incoming sunlight, and air ducts that are integrated into the flooring to allow for localised control of air circulation based on occupancy levels.
Schlueter said that in Singapore, where cooling and ventilation accounted for 70 per cent of the total energy consumed by the building sector, this “new set of solutions for air conditioning and lighting could halve both space and energy requirements, which could achieve significant savings to building material costs and energy bills.”
He noted that this cost savings potential has been largely untapped by the green buildings sector thus far.
Helmut Macht, chief technology officer of Siemens Building Technologies, which is also contributing expertise to the 3for2 project, expressed confidence that “Singapore, with its affinity for innovation, will become a catalyst and role model for transferring these principles and operational concepts to high density tropical areas.”
Building green in tropical cities
SEC FCL hopes that the UWCSEA office is the first step to scaling the technology up for widespread commercial use in the tropics. It calculated that a hypothetical 50-story building in Singapore that adopted the technology could achieve a 0.6 metre reduction in floor-to-floor height and reduce structural costs by one third, and maximising the building space could translate to an additional S$318,000 in rental revenue.
However, Rysanek said that the road to making this a reality was a long one. “Before we can really consider applying our concept throughout a 50-storey skyscraper, we need to make sure we get the basics right. With our project at UWCSEA, we have to first prove that our system will deliver the most energy efficient office space in the region”. He added that challenges such as minimising condensation on the cold PCBs still needed to be addressed.
Schlueter told Eco-Business that while the office will not achieve the full range of potential benefits such as space savings due to its small scale, it is a crucial exercise to demonstrate the commercial viability of the 3for2 concept to developers.
The facility is fitted with sensors to collect data on energy usage, which will then be run through a cost calculator project to make an economic case to developers in Singapore and the region, shared Schlueter.
The project at UWCSEA was slated to run till the end of 2018, but initial findings on energy and cost savings would be analysed in mid-2016, added Schlueter.