Decarbonising Pan Brothers, one of Indonesia’s largest garment manufacturers, was never going to be easy.
The 43-year-old firm that makes outdoor clothing and sportswear for brands such as Adidas, Uniqlo, Lacoste and The North Face started out on the long road to net zero by calculating its baseline emissions last year.
Pan Brothers has 10 subsidiaries, 23 factories and 29,000 employees that make 117 million pieces of clothing a year for export to the United States, Europe and elsewhere in Asia Pacific, its biggest market, generating US$690 million in sales.
The company will need to reduce its emissions to stay competitive in increasingly carbon-conscious global supply chains. In 2018, the garment and textiles industry committed to cut emissions by 30 per cent by 2030, a pledge that has pressured firms all along the supply chain to trim the carbon cost of a sector that accounts for 6 to 8 per cent of global emissions.
A large chunk of Pan Brothers’ emissions comes from running its factories, but the company’s Scope 3 emissions – indirect emissions from the value chain that are hardest to control – is the biggest portion of its carbon footprint.
“
Textiles are not as sexy as nickel in Indonesia right now.
Satrio Boediarto, general manager, business development, investor relations and sustainability, PT Pan Brothers Tbk
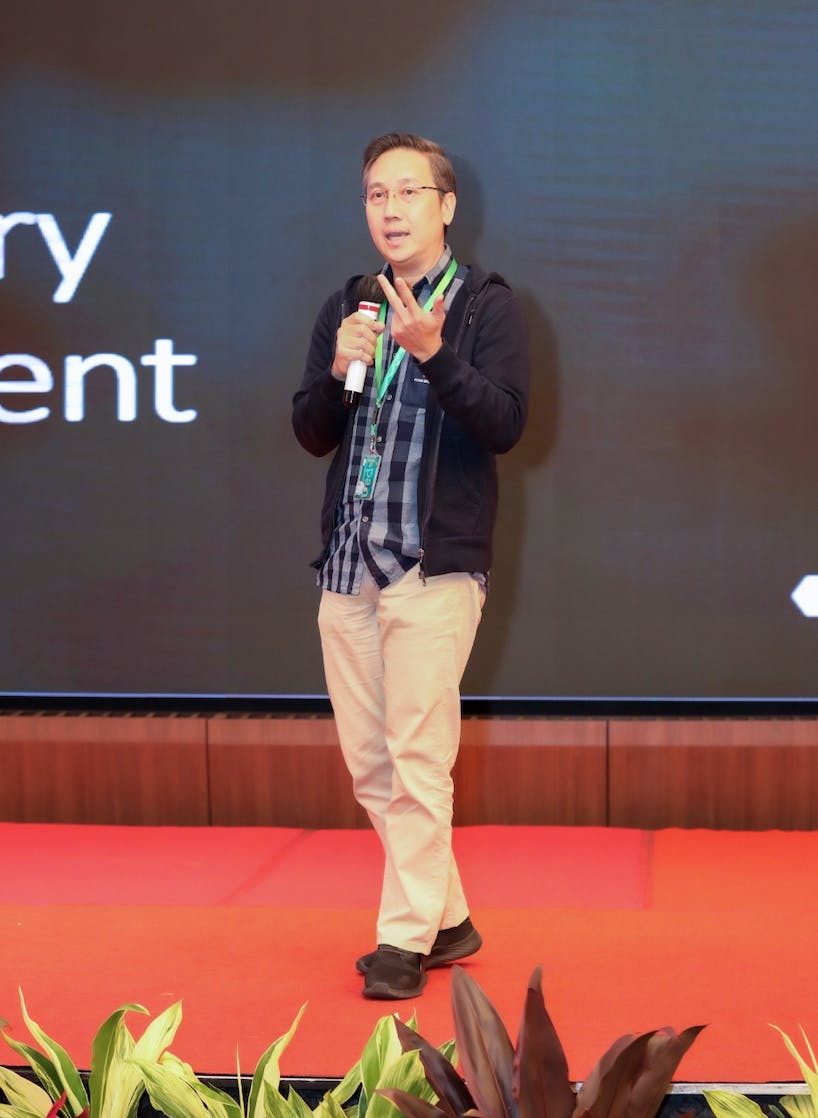
Satrio Boediarto, Pan Brothers’ general manager of business development, investor relations and sustainability
Pan Brothers imports 84 per cent of the 3,985 different types of fabric it uses from overseas, for instance polyester from China, Taiwan and Japan, to make outdoor clothing and sportswear. This comes with a considerable carbon cost, says the firm’s general manager of business development, investor relations and sustainability Satrio Boediarto, who usually goes by his shorter familiar name, Boedi.
Pan Brothers would like to source more material locally, to curtail its carbon footprint, but Indonesia’s struggling domestic textiles sector cannot supply the materials the company needs. Indonesian textile exports fell by a quarter last year and the industry has been going through a period of sustained decline.
“We see a lot of interest from Chinese textiles firms who want to come to Indonesia and build fabric mills. This would reduce our emissions as we would not have to import so much fabric. But these investments must be supported by the government, which does not consider textiles to be as sexy as nickel,” says Boedi, referring to the huge interest in Indonesia’s reserves of a highly sought-after mineral used in clean energy technologies.
Pan Brothers has taken strides to clean up the electricity that powers its factories to reduce its Scope 2 emissions. But electrification presents the company with a challenge shared by all of the large local firms that joined the Indonesian Chamber of Commerce’s (KADIN) Net Zero Hub last year – a cap on renewable energy procurement.
Indonesia’s state power company, Perusahaan Listrik Negara (PLN), has capped the amount of renewable energy companies are permitted to use, because the grid is oversupplied with coal-powered electricity. “We cannot install more than 15 per cent of our electricity capacity with solar. We want to procure more renewables, but we won’t be able to get a permit,” says Boedi.
The company is also trying to decarbonise the transport its employees uses – another big part of its carbon footprint – but since Indonesia’s electric vehicle (EV) infrastructure is still in its infancy, EVs are not a realistic option to shuttle employees around, says Boediarto. Hybrid vehicles are the preferred solution for now, he says. he said.
Meeting the company’s net-zero target will require investment, which may prove difficult to secure given its financial health. The company was hit hard by the Covid-19 pandemic and has struggled with debt. In April, Pan Brothers approached banks to refinance its loans. New models for financing solar power on its factory rooftops, which do not require upfront investment, have helped the company keep the costs of the transition to cleaner energy sources down.
In this interview, Boediarto talks about why the company’s employees are its the top sustainability priority, what motivates the firm to decarbonise, and how the company is being affected by climate change.
What motivated Pan Brothers to decarbonise? Is the company under pressure from European or American customers to reduce emissions or are looming carbon border taxes an issue?
There is no pressure from the brands at the moment. Although we set a net-zero target last year, our sustainability journey started in 2015 long before the net-zero movement, with the construction of our new “green” head office in Boyolali, Central Java. It is platinum green building-certified; we recycle rainwater for sanitation and save energy through energy-efficient lighting.
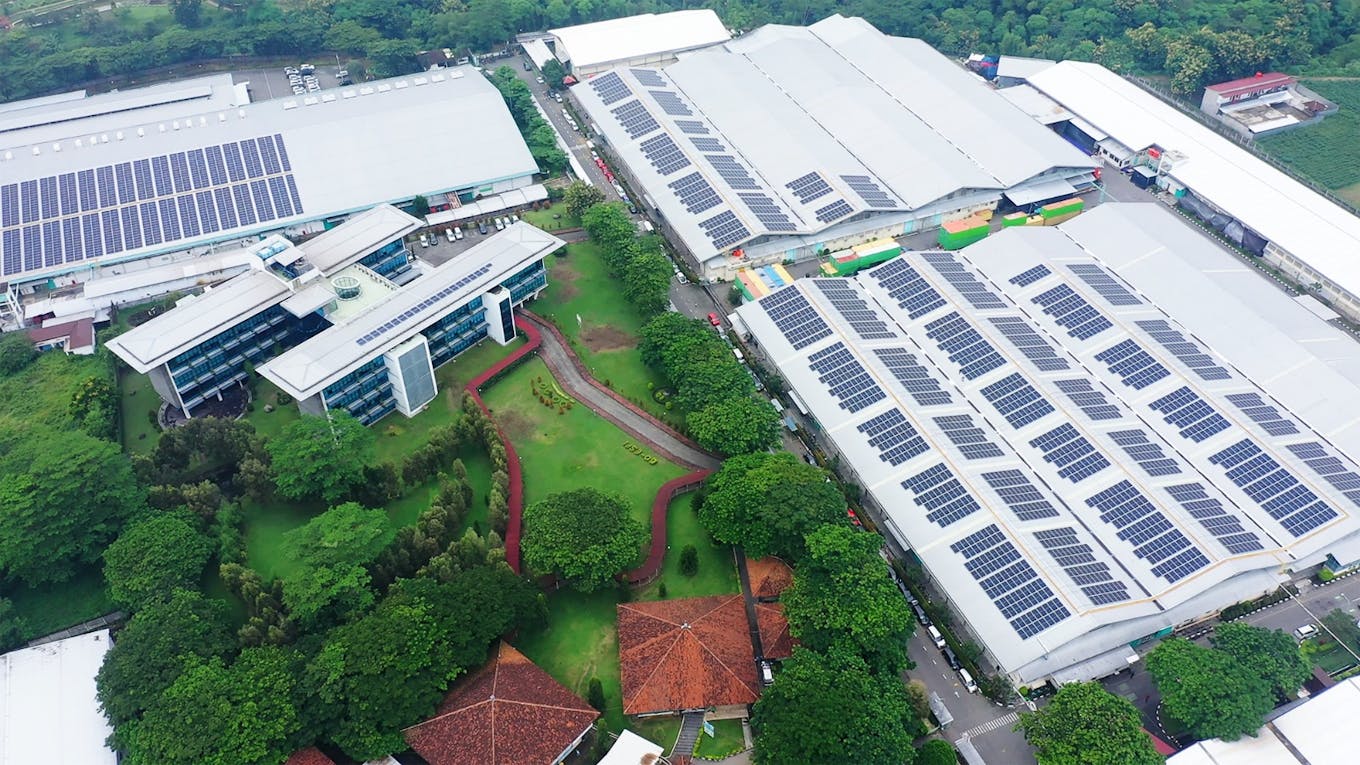
Pan Brothers main factory in Boyolali, Central Java, is partly solar-powered. Image: Pan Brothers
In 2021, we put solar panels on our rooftops to reduce the reliance on coal for power. The first installation was 1.8 megawatts (MW) of capacity on three factories, and we plan to add another 1.2 MW this year. We’re also looking to upgrade our boilers, so that they can burn biomass as well as fossil fuels, to reduce our emissions. However, where we source biomass from will be a challenge, as will be cost. Sourcing biomass from faraway islands will not make sense as that will add to the transportation footprint.
Initially, we thought about electric vehicles, but to be honest the infrastructure just isn’t there yet in Indonesia. So we’ve opted for hybrid vehicles, which can reduce emissions by 34 per cent compared with internal combustion engine vehicles. We have 29,000 employees and their transport (emissions) is part of our Scope 3 emissions.
What is your main sustainability priority as a business? How has the company been working to improve human rights to ensure that it complies with global supply chain standards?
Adopting the Sustainable Development Goals (SDG) framework has been crucial for us to identify the key focus areas. For garment manufacturers, the main focus is the social side of sustainability.
We follow government regulations, and all of our workers are paid above the minimum wage [according to the latest data, the minimum wage for Indonesia’s manufacturing industry is an average of IDR 2,963,061 per month, or US$195]. We also work to take care of the communities that surround our factories. Although we have 29,000 employees, we have perhaps 60,000 people to take care of. For example, the ‘Canteen Project’ is a partnership with local food vendors and canteen owners in the local community in Boyolali, many of whom operate out of our facility, providing nutritious, affordable food. We also donate scrap fabrics to local businesses, so they can be repurposed and sold on.
“
Net-zero is a mindset.
We want our people to live healthy lives, have access to clean water, a safe workplace, good medical coverage, higher education, training and so on. We want them to be part of our decarbonisation journey, as a company. Net zero is a mindset which has to start with our people.
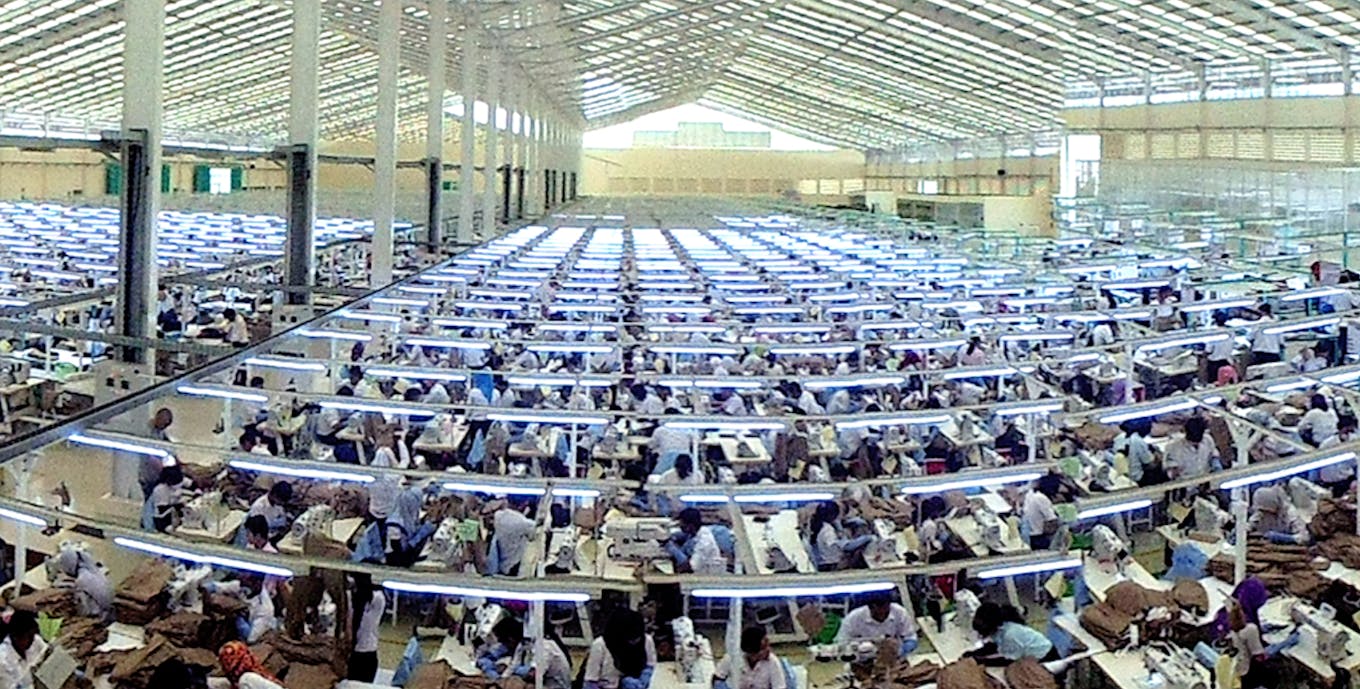
Inside Pan Brothers main factory in Boyolali, Central Java. Image: Pan Brothers
What’s the biggest challenge the company faces in decarbonising?
The main one is that the national power company [PLN] restricts how much renewable electricity we can buy. We cannot install more than 15 per cent of our electricity capacity with solar. We want to procure more renewables, but we won’t be able to get a permit, because of an oversupply of energy from the grid. We can buy renewable certificates, but they are also provided by PLN.
Another challenge is our Scope 3 emissions. We import almost all of our materials. We only source about 15 per cent locally. It would be great if China invested in Indonesia and built a fabric mill here. That would reduce our emissions as we wouldn’t have to import so much material. After Covid-19, we’ve seen a lot of interest from Chinese companies to come here invest, but this has to be supported by the government. Also that’s a challenge. The government doesn’t see the textile industry as sexy as nickel.
In 2008, Indonesia has a really advanced textile industry. We had the latest technology then and produced very good fabric. But legislative changes made it easier to import material. Fewer firms produced fabric themselves, and many people tried to turn a quick profit as brokers by importing textiles from overseas. Since then, Indonesia’s textiles industry started to lag behind other countries such as China, India and Vietnam. India has a Ministry of Textiles, which shows their commitment to the sector. Indonesia doesn’t have one.
Pan Brothers has experienced financial difficulties in recent years, particularly during the pandemic. How has the company been able to fund the decarbonisation plan?
What I can share is that our customers have supported us during the pandemic, which is why we’ve been able to invest in the sustainability plan. A close relationship, mutual understanding and transparency with buyers has been key.
Also, the cost of solar energy has fallen considerably, and technology is evolving so quickly bringing down costs further. That said, we have to make sure that what we invest in our sustainability plan does not impact the whole business. The business has to grow and we have to make a profit.
One issue is that the banks are not ready for sustainable finance and supporting businesses making the transition. Hopefully, the ecosystem will mature so that businesses can secure lower interest loans for sustainability programmes.
How is the business being affected by climate change?
It depends on the location of our factories. Our main factory, in Boyolali, Central Java, is high above sea level and surrounded by mountains. At the moment, we’re not experiencing severe climate impacts, but we need to be prepared. Ten years from now, things could be very different. We are in the process of assessing the resilience of our factories and where they are located to ensure our operations are climate resilient.
For more Indonesia ESG and sustainability news and views, subscribe to the Eco-Business Indonesia newsletter here.