By the end of the year, a new skyscraper called CapitaGreen will rise in the heart of Singapore’s Central Business District and add to its skyline. But unlike its peers, this new Grade A office development has one distinguishing feature – it is the first high-rise building in Singapore that uses a unique high-strength concrete that could revolutionise the way skyscrapers are designed and built.
The 40-storey building, located at 138 Market Street, is jointly developed by CapitaLand, Capita Commercial Trust, and Mitsubishi Estate Asia. Six floors with 29 columns will be made with a special grade 100 ultra-high strength concrete supplied by Holcim Singapore, a leading supplier of concrete and part of the wider Swiss-headquartered Holcim Group, the world’s largest cement maker.
This ‘Supercrete’, says Holcim Singapore chief executive Sujit Ghosh, enables the industry to “build more with less”, as it significantly reduces the amount of concrete required, thus saving energy and manpower. In fact, using high grade concrete enables building owners to score points under the Building and Construction Authority (BCA) Green Mark rating system, which ranks buildings for its environmental performance. BCA is Singapore’s construction industry regulator.
While local regulations now allow the usage of concrete up to grade 105, most buildings in Singapore are constructed using concrete grade 30 to 50. The grade refers to the capacity to withstand loads - the higher the number, the higher the load it can withstand.
According to Holcim and BCA Pillars magazine, a replacement of grade 40 concrete with grade 100 concrete can reduce the concrete volume needed by about 45 per cent, and strengthens the durability of the structure, extending the lifespan of the building.
“
Their saleable floor space also increases when they use high grade concrete, because it enables smaller columns and hence the net floor area is bigger and building owners can sell that additional area
Even though Supercrete makes up only 1 to 2 per cent of CapitaGreen’s total concrete use, Holcim’s Sujit Ghosh welcomes it as a “good start”. In this interview, he speaks to Eco-Business on why he thinks it is only a matter of time before the industry adopts this to improve sustainability and design.
Since Supercrete was launched, how has the industry received this new product?
A couple of years ago, the code of practice here changed to allow up to grade 105 concrete - up from grade 60. Since then, the take up has been slow even though high grade concrete can reduce materials consumption by almost half.
The industry is not used to it and engineers do not know how or are hesitant to design with higher grade concrete, but of late, we have seen movement in the right direction.
CapitaGreen is the first adopter here, the decision was made by its designers, RSP architects. Even though only one to two per cent of the concrete required is provided by Supercrete, we are happy as it is a start. People will get used to it over a period of time.
We have other high-rise projects in Mumbai and Delhi in India which have started using such high grade concrete, so the industry worldwide is moving in that direction. In some other cities such as Tokyo and Hong Kong, where buildings are typically built tall, the use of high grade concrete is already prevalent.
What are some other benefits of using Supercrete compared to its conventional peers?
Some developers want to differentiate their buildings and it helps with their sustainability efforts. Their saleable floor space also increases when they use high grade concrete, because it enables smaller columns and hence the net floor area is bigger and building owners can sell that additional area.
It can be used for all aspects of building, but engineers especially like to use it in columns of high-rise buildings because the higher the building, the larger is the load on the columns, due to the weight of the building.
Typically, the columns and beams at the lower floors are thick and big because it has to withstand the weight, but using Supercrete, builders can make them 40 to 50 per cent more slender.
What do you think are the challenges in getting the industry to accept it?
Well, there is a lot of inertia in the construction industry. Many think “why should I change?”
We would like to see it being used more prevalently, and for this to happen, we have to go back to the engineer fraternity as they are the ones that have to be open, receptive and daring. If they are not open to new design concepts and be bold in their designs, the contractors will just follow the old practice.
So we do reach out to them, and help them be aware of the possibilities – that they should not just copy and paste the specifications from a previous building and make cosmetic changes, but change the way they think of and design a building.
Our hope is to see building designers as leaders in enhancing sustainability. I hope we can eventually see the buildings in Singapore using Supercrete for 10 per cent or more of its concrete needs.
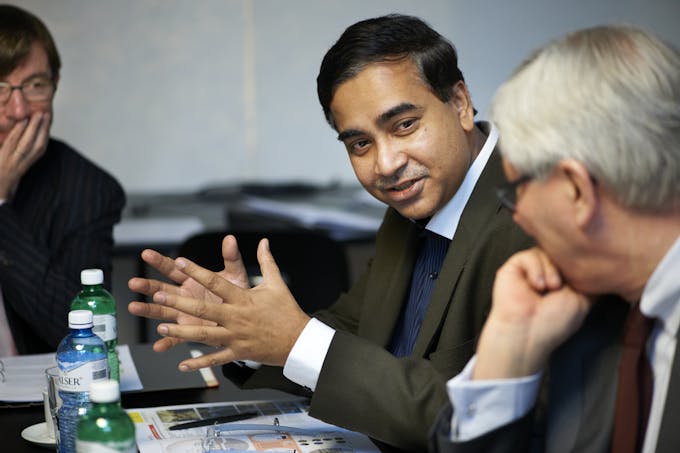
Holcim Singapore chief executive Sujit Ghosh
Here, government policies can play an effective role in getting things going. Take Easecrete as an example. It is a green self-compacting, self-levelling concrete that minimises the problems of conventional concrete production that is laborious, time-consuming.
We launched Easecrete two years ago, and even though it costs 30 per cent more than the conventional concrete, it is selling like hotcakes now. It has been proven to save time and costs that far outweigh the higher initial unit cost, such that public agencies such as the BCA and the Housing and Development Board (HDB) have been encouraging contractors to use it.
This high grade concrete is double the price of normal grade concrete. Is this cost inhibitive for the industry to adopt widely?
Well, yes it is expensive on a per unit basis, but you also halve the raw materials needed. Looking at the larger picture, you gain workable space, and the project is also more sustainable because you’re consuming less resources - not just materials, but also the associated chain of activities such as number of men needed on site, and time required to lay the concrete. So finally, from a total net cost analysis, the use of high grade concrete is actually cost-effective and not expensive.
We launched this product with the philosophy “build more with less” - we’re not saying build less because in Singapore, building less is against the country’s direction.
How does the footprint of Supercrete compared with its peers?
Well, it needs more cement to make it is stronger. However, we use slag cement and various chemicals in the concrete mix to reduce the consumption of cement and enhance the performance.
During the development of Supercrete, we found that Supercrete and other concrete with alternative materials actually having a significant lower carbon footprint compared to the conventional concrete. In comparison, the introduction of cement slag in concrete mix lowers the CO2 emission by 45 per cent or about 274 kg per m3.
How long did it take for Holcim Singapore to develop this?
Our in-house researchers took more than six months in 2009 to develop it. We have a Centre of Excellence in Singapore set up in collaboration with the Economic Development Board – which is the first for Holcim in Asia – which looks into product innovation to solve challenges such as scarcity of space, materials and increase sustainability.
We would like to export these solutions to the region eventually, but we do face challenges in that the requirements and conditions of the construction industry vary drastically from country to country so many solutions that are developed in Singapore may need some tweaking to be adapted to the local conditions, and we are able to assist such needs.
Together with public sector partners, Holcim has been discussing this idea of a “pre-project innovation lead” which will bring all the relevant players such as architect, design engineer, builder to sit at the table at the design stage to decide how best to design a new project.
If we do this, then we can make the building as sustainable as possible right from the beginning.