Pumps are not the most glamorous or accessible technology but modern, urban life as we have known it for the past two centuries could not have existed without them.
Present whenever liquid needs to be circulated, pumps are all around us in buildings, reservoirs, swimming pools, dams, garden sprinklers and fire hydrants, among other locations.
It may come as a surprise to many people that pumps collectively consume as much as 10 per cent of global electricity; because of their ubiquity, they require huge amounts of electrical energy to run and so a significant carbon footprint occurs.
Grundfos, the world’s biggest supplier of pumps say if all pump systems were switched to high efficiency ones, this could reduce 4 per cent of the world’s total electricity consumption.
Today, much of the energy consumed by pumps and pump motors go to waste, says Grundfos. This is because most pumps currently installed are larger than necessary and they run continuously at their top speed regardless of actual requirements.
In reality, most pump motors only need to run at their full speed 5 per cent of the time, and this is true for all kinds of pumps: in commercial buildings, industrial applications, public buildings and water utilities.
This means there are major opportunities for energy savings by using technologies that are more intuitive and allow for automated speed adjustment, depending on how much energy it needs, says Grundfos.
These solutions already exist today, and although some upfront cost is required, energy savings are immediate and the payback time can be as short as 2 years.
In Vietnam, Grundfos helped the Ca Mau Municipal Water Supply Company achieve substantial energy savings after surveying its existing ground water pumping station.
During a visit in May to the company’s ground water pumping station in the Mekong Delta, the Grundfos team was surprised to detect an abnormal vibration on the discharge pipe even though it was only producing 45 cubic metres of wateran hour. One possible cause was the motor size.
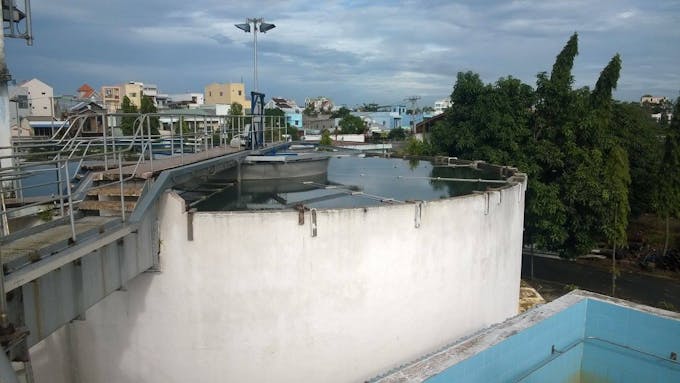
A project by Grundfos in Vietnam. Image: Grundfos
The team soon discovered that the motor size was too big for the 30 kilowatts (KW) pump. This was wasting energy.
Together with the technical department, Grundfos eventually conducted an energy check for all of the company’s 53 wells to evaluate its energy consumption.
Following the energy check, Grundfos conducted a seminar for 60 of the municipal company’s engineers covering the basic elements of a ground-water pumping system, energy consumption calculations and energy check tools and methodology.
The checks showed that with the plant’s production capacity of 53,000 cubic metres in a day, the total daily power needed was 17,490 kW per day, or the equivalent of 0.33kw per cubic metre.
This was a very high figure. Grundfos found that the company can effectively reduce its energy consumption to 0.21kw per cubic metre just by replacing the old pumps with appropriate ones and modifying the pumping stations.
Just one month after installing two Grundfos pumps – called the SP46 and SP60 – the water company achieved the savings that Grundfos projected.
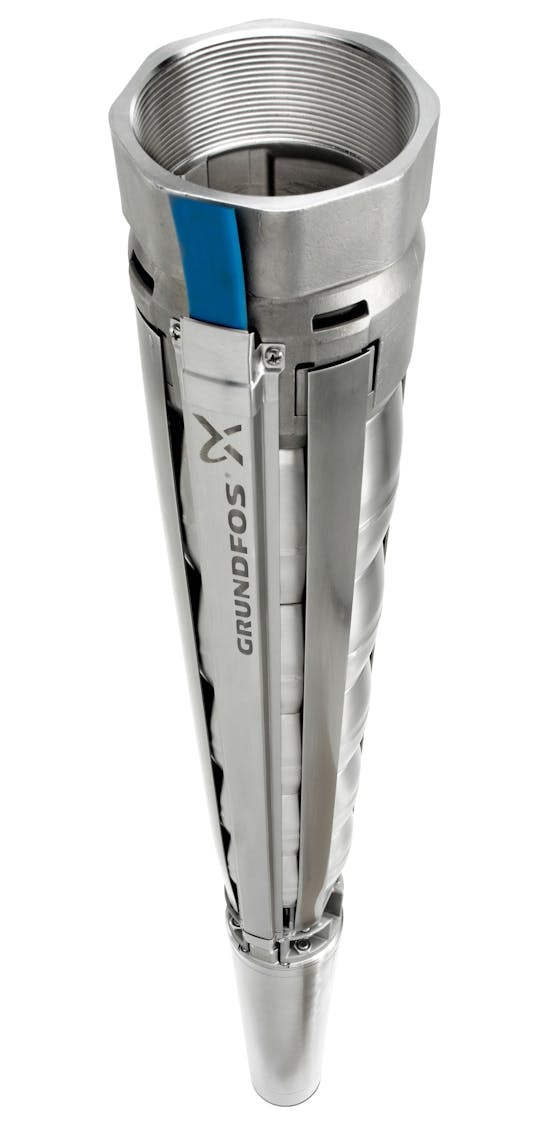
Grundfos’ water pump. Image: Grundfos
A comparison with other brands convinced the water company that Grundfos’ SP pump is an efficient solution with a long lifespan. Furthermore, good reviews by many municipal water supply companies in the Mekong Delta that have been using SP pumps for many years also influenced Ca Mau’s decision to make the switch.
The firm is now considering making further investments in multiple phases, partly funded by company funds and money from the energy savings, says Ly Hoang Trung, director of Ca Mau Municipal Water Supply Company.
When completed, the Grundfos SP pumps can reduce the company’s energy consumption by 6,000kw/day which is equivalent to 3,800,000,000 Vietnamese dong (US$169,100) a year, he adds.
“This improvement is vital for the company,” Ly says “Although the investment is huge, estimated payback time is 2 to 3 years and Ca Mau Municipal Water Supply Company strongly believes the savings from switching to Grundfos will pave a better future for the company.”